St. Pauli Elbtunnel
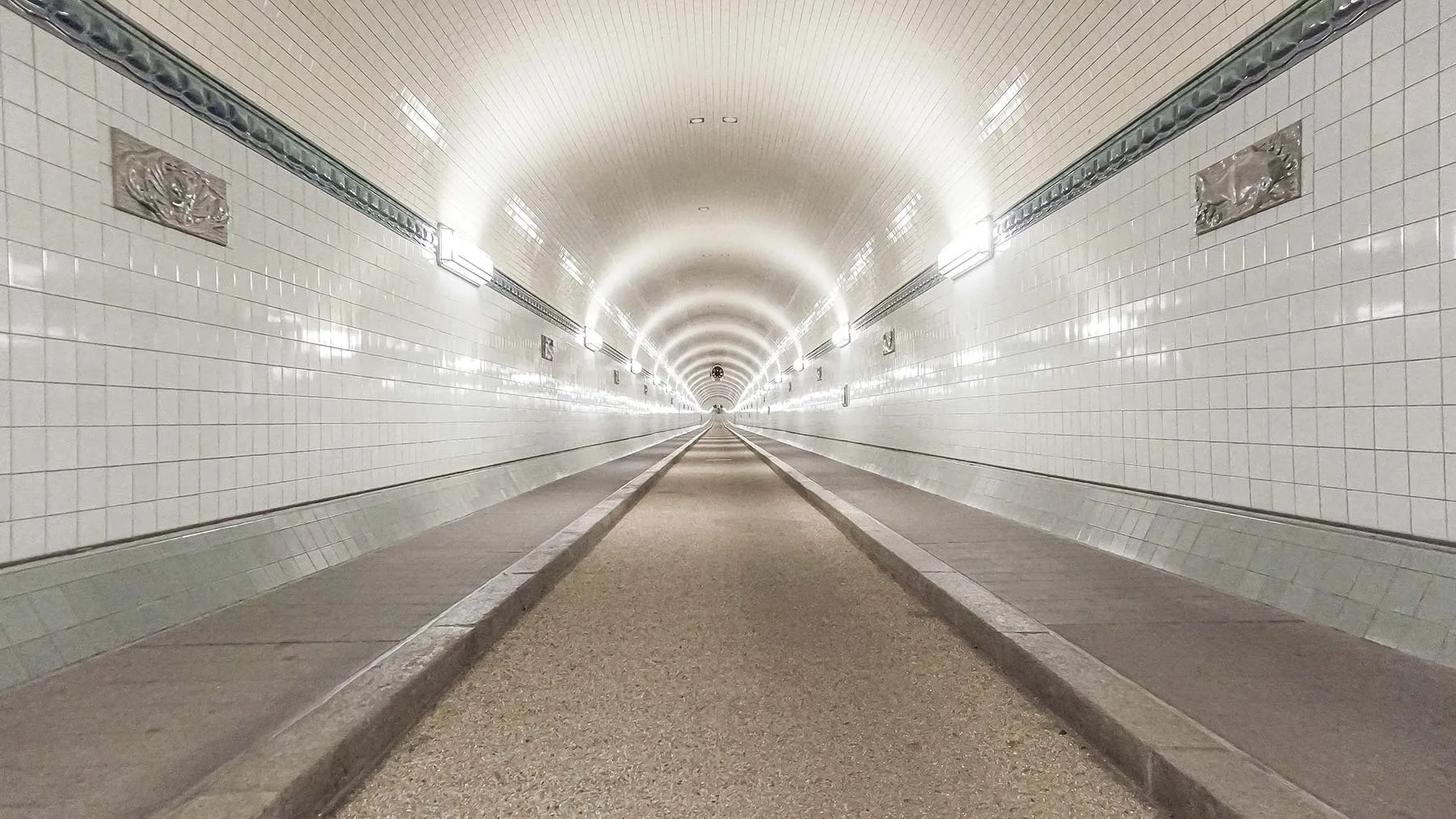
High density concrete counters hydrostatic pressure
When a historical, and much loved, underwater tunnel required full renovation, MagnaDense high density concrete was the ideal solution to counter the hydrostatic pressure that could have had catastrophic consequences!
Originally opened in 1911, the St. Pauli Elbtunnel was an essential part of Hamburg’s transport infrastructure, connecting central Hamburg with the docks and shipyards on the south side of the river Elbe. It also quickly became a deeply loved landmark and tourist attraction.
St. Pauli Elbtunnel Facts
It is Europe’s first underwater tunnel. Built by 4,400 workers it was opened in 1911. 24 metres below the surface of the River Elbe, it needs high density concrete to prevent it from rising up!
426 metres long, St Pauli Elbtunnel consists of two parallel 6 metre diameter shafts – one eastbound and one westbound. Each shaft is constructed from 1,700 ring-shaped steel beams held together with 200,000 rivets and bolt fasteners, covered with concrete and finished with 400,000 tiles.
Extensive renovations require an innovative solution
After 100 years of service, the Elbtunnel required extensive renovation and that’s where we came in. 24 metres below the surface of the river Elbe, hydrostatic pressure is a major concern. Without achieving a suitable density, the tunnels could rise up causing serious problems. Hydrostatic pressure could be alleviated by adding ballast on the riverbed, but this would reduce the depth of the river restricting ships with large hulls. The tunnels themselves therefore needed to achieve the desired density.
High density concrete to the rescue
Lead plates had been used in the original construction. For environmental and health issues these had to be replaced. There wasn’t enough space to line the tunnel walls with standard concrete of a sufficient density. High-density concrete was put forward as the ideal solution with MagnaDense as the aggregate. This would compensate the buoyant force, allowing structural clearance to be preserved.

We also have to ensure that the tunnel is heavy enough at every phase of the project. If the tunnel gets too light it would rise and then it would be in danger.
There was, however, one big challenge! How to get the high-density concrete from the surface deep into the tunnel?
Tunnel renovation work commenced with the east tunnel and was a joint venture between HC Hagemann GmbH & Co. KG, Ed. Züblin AG and the ready-mixed concrete company Thomas Beton GmbH. The setup was designed using a mobile concrete pump above ground which was facilitated by Betonlift GmbH & Co. KG.
I needed to make the different parties understand that pumping high density concrete was the most effective solution in this project…because of our many references and experience with heavyweight concrete in general, and in tunnels in particular, MagnaDense was chosen to produce the heavy, dense concrete used for the invert of the tunnel.
Record-breaking pumping installation
The pipe was guided through the vertical shaft of the tunnel. Connected to this, a horizontal pumping pipe was installed over half the length of the tunnel up to the centre. This long pipe resulted in a national record in terms of the pumping length. Once one side was finished, the same procedure was repeated at the other side.
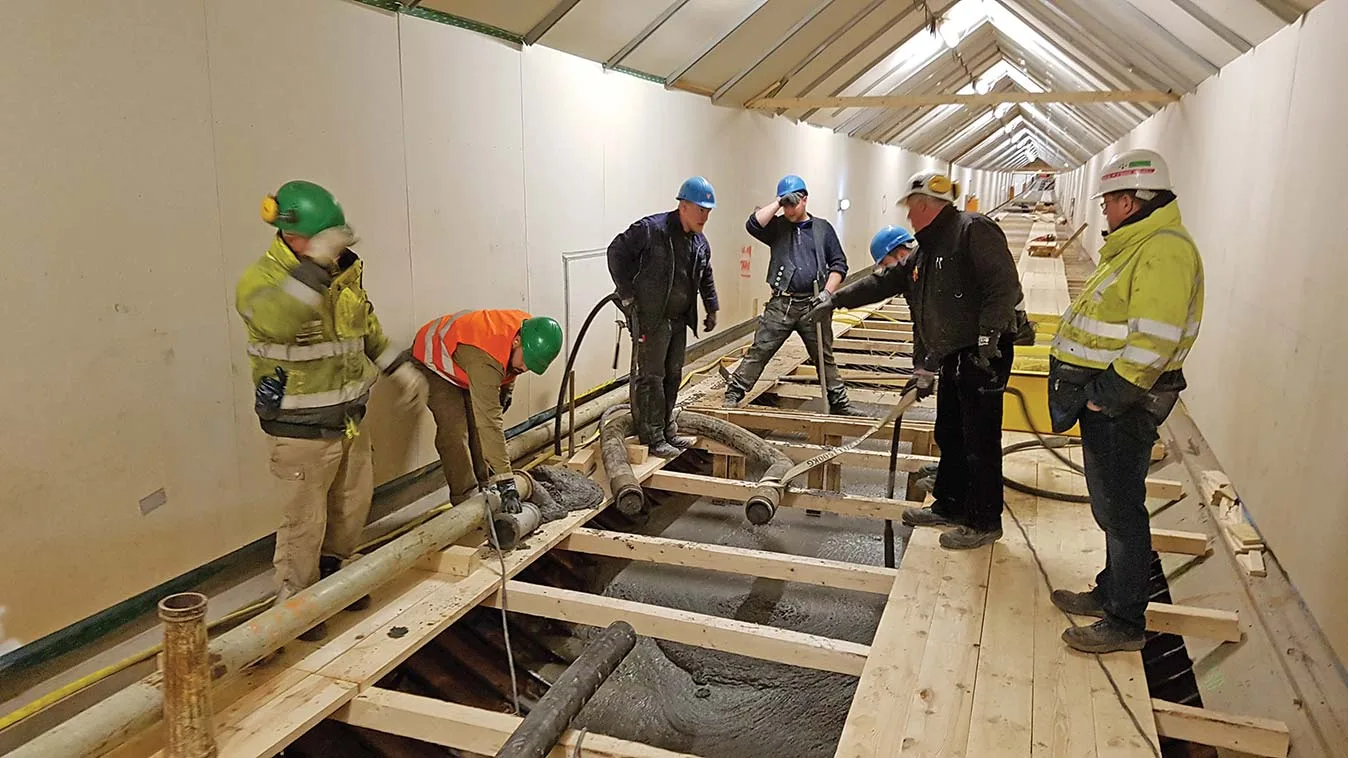
During the concreting operation, this pipe was dismantled backwards as the inverted concrete was placed towards the shaft. The pump was fed by Thomas Beton GmbH using up to four truck mixers in a shuttle service.
We worked closely with stakeholders to produce the ideal mix. Using MagnaDense, a density of 3.6t/m³ was produced. The secret of successful pumping was the bespoke concrete composition that was achieved with a specific mix design, together with slow pumping using the latest technology.
There's nothing like it anywhere in the world. Tunnel technology, as well as a historical monument, that can actually be used. I think you can see that the effort was worth it. The teams of people who've worked on the tunnel are all very proud. I've seen them today looking very pleased and that makes me even happier.
Over 1,400 tonnes of MagnaDense was used for the renovation of the east tunnel alone.
With the need to pump high density concrete to the centre of the 426 metre long tunnels, pre-planning and coordination between all key stakeholders was essential to ensure a successful renovation. This resulted in a national record for the pumping distance of concrete.
High density concrete, produced with MagnaDense, is no harder to handle and install than standard density concrete. No specialist equipment or training is required.
St. Pauli Elbtunnel has been restored to its former glory, delighting the Hamburg residents who fought hard for it to be preserved.
Facts about MagnaDense
Compliance with Standards: EN 12620 and DIN 6847-2
Particle Density (dry): 4.8 – 5.1t/m3
H2O Absorption: <0.3 %
Particle Shape: Angular
Surface Texture: Rough